Planning a new building or upgrading an old one? If your project needs better vertical movement for people or goods, it’s time to think about install an elevator.
Installing an elevator is a big job. This guide will walk you through the main elevator types, key parts, site preparation steps, and the full installation process—so your project can move forward smoothly.
Types of Elevator Systems
Elevators carry people or goods between floors using different lifting methods. When you plan to install an elevator, it is important to know the common types available. Your choice will depend on the building height, space, and budget.
Traction Elevators
Traction elevators use steel ropes or belts connected to a counterweight. A motor moves the ropes to raise and lower the car. They are common in mid- to high-rise buildings because they are fast and energy-efficient. But, they usually need a machine room and can be harder to install.
Machine Room-Less (MRL) Elevators
MRL elevators are a type of traction system that does not need a separate machine room. The motor is placed inside the shaft, saving space. They are energy-efficient and good for buildings with limited space, but can be more expensive to service.
Hydraulic Elevators
Hydraulic elevators use a piston and fluid to lift the car. They are often used in low-rise buildings and are easier to install where tall shafts are not possible. They are slower and use more energy, but cost less for short travel distances.
Pneumatic Elevators
Pneumatic elevators use air pressure to move the car up and down inside a tube. They are small, quiet, and do not need a pit or machine room. They work well for homes but are not ideal for heavy loads or tall buildings.
Screw-Drive Elevators
Screw-drive elevators move the car using a rotating screw and a motor. They are simple in design, quiet, and reliable for low-rise use. But, they are slower and not suited for heavy traffic areas.
Types of Elevator Systems by Application
Earlier, we explained the main elevator system types and how they work. When you plan to install an elevator, it also helps to think about where it will be used. Common examples include:
-
Passenger elevators for homes, offices, and public buildings.
-
Freight elevators for moving goods in warehouses, factories, or malls.
-
Residential elevators for private houses with limited space.
-
Hospital elevators for beds and medical equipment.
-
Automobile elevators for parking garages or car showrooms.
Choosing the right type depends on both the system design and the intended use.
Components of an Elevator System
An elevator system has several main parts that work together to move people or goods between floors. When you plan to install an elevator, it helps to know what each part does.
-
Cabin (Car): The enclosed space where passengers or goods are carried. It is designed for comfort, safety, and capacity.
-
Hoistway (Shaft): The vertical space in which the elevator moves. It includes guide rails to keep the car steady.
-
Drive System: The machinery that moves the elevator, such as traction ropes, hydraulic pistons, or screws.
-
Counterweight: A weight that balances the car’s load, reducing the power needed to move it.
-
Control System: The electronics that manage speed, direction, and stopping at the right floor.
-
Doors: Automatic doors on both the cabin and each floor, designed to open and close safely.
-
Safety Devices: Brakes, buffers, and sensors that protect passengers and prevent accidents.
Knowing these components can help you choose the right design and prepare for a safe, efficient installation.
Assessing Your Building’s Elevator Needs
Before you decide to install an elevator, it’s important to know if your building really needs one and how many elevators would work best.
Determining the Need for an Elevator
You need an elevator if your building is tall, busy, or must meet local accessibility laws. For example, if your building has more than three floors, or if it serves people who have difficulty walking, an elevator becomes necessary. Accessibility rules from local government or international bodies often need elevators to ensure everyone can use the building safely.
Deciding How Many Elevators You Need
The number of elevators depends on how tall the building is and how many people use it. Small residential buildings with five floors or less usually need only one elevator. Buildings that are taller, like mid-rise offices with six to twelve floors, often have two to four elevators to avoid long waits. High-rise buildings with more than twelve floors and lots of traffic may need more elevators, sometimes one elevator for every 70 to 90 people during busy times. Big elevator companies like Otis, Schindler, and Mitsubishi use these numbers when designing elevator systems.
Evaluation Factors
To decide how many elevators to install, you should think about several things. First, the total number of floors and the building’s height affect the need. Then, consider how many people will use the elevators at busy times. Also, check local building codes and accessibility laws that apply. The type of building matters too, since homes, offices, hospitals, and stores all have different elevator needs. Lastly, your budget for installation and maintenance will influence how many elevators you can afford and maintain.
Average Installation Costs for Different Types of Elevators
The cost to install an elevator depends on the type of elevator, building size, and other factors. On average, expect to pay between $20,000 and $50,000 for a hydraulic elevator, $30,000 to $70,000 for a traction elevator, and $40,000 to $80,000 for a machine room-less (MRL) elevator.
Extra Expenses To Consider
Besides the basic installation cost, you should also think about other expenses. Building or modifying the elevator shaft can increase the price. Electrical upgrades may be needed to support the elevator’s power requirements. Local permits and inspections are often required and can add to the cost.
Cost information is based on recent industry reports and may vary by location and project.
Selecting the Best Elevator for Your Building
When you decide to install an elevator, choosing the right one is key for safety, convenience, and cost-effectiveness. To make the best choice, consider these important factors.
Building Size and Usage
First, think about how tall your building is and how many people will use the elevator. Buildings with more floors or many occupants need elevators with higher capacity and faster speeds. For smaller buildings or homes, compact elevators with lower capacity may be enough.
Accessibility and Safety
Your elevator should meet local building codes and accessibility laws. Features like wide doors, smooth rides, and emergency communication systems help ensure safety and ease of use for everyone, including people with disabilities.
Energy Efficiency and Technology
Modern elevators often include energy-saving features like variable-speed motors and standby modes. Choosing an energy-efficient model can lower operating costs over time and reduce environmental impact.
Preparing Your Building for Elevator Installation
Preparing your building properly can make the process to install an elevator smoother and avoid problems later.
Inspecting Existing Structures
Check the current building structure to see if it can support an elevator. Look for any weaknesses in walls, floors, or shafts that might need repair or reinforcement. Fixing these issues before installation helps keep the project on schedule and safe.
Planning the Elevator Shaft and Machine Room
If your building doesn’t have an elevator shaft, you will need to plan and build one. This can be a complex task that requires careful planning to fit the building’s layout. The machine room location must also be decided to allow easy access for maintenance.
Choosing Installation Locations
Decide where to place the indoor elevator car and the outdoor machine room (if needed). The location affects the elevator’s performance and convenience. Avoid spots that block natural light or limit space for users.
Getting Necessary Permits
Before starting work, make sure you or your contractor has secured all required permits and inspections. Local laws often need official approval to ensure safety and compliance.
Elevator Installation Process
Installing an elevator involves several key steps, each important to make sure the elevator works safely and correctly. On installation day, the process usually follows this timeline:
-
Site preparation: Workers prepare the elevator shaft and machine room, making sure everything is ready for installation.
-
Installing elevator parts: The elevator car, cables, and control systems are put into place inside the shaft.
-
Electrical connections and testing: Technicians connect the elevator to power and test all its functions to ensure safety.
-
Final inspection: Local inspectors check the elevator installation to confirm it meets safety standards.
The entire installation typically takes between two and six weeks, depending on the building size and elevator type.
Solutions for Buildings Without a Pit, Machine Room, or Indoor Shaft
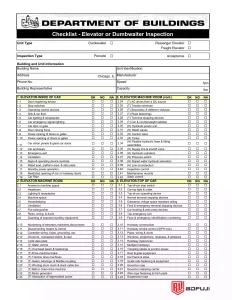
If your building cannot have a pit dug, a machine room built, or an indoor elevator shaft, there are alternative solutions to install an elevator.
-
Machine Room-Less (MRL) Elevators: These elevators do not need a separate machine room. The machinery is compact and placed inside the shaft, saving space and allowing easier installation in buildings with limited room.
-
Hydraulic Elevators Without a Pit: Some hydraulic elevators use a special system that does not need a deep pit. This makes installation possible even in buildings where digging is difficult.
-
Outdoor Elevator Shafts: When indoor shafts are not possible, an elevator shaft can be built outside the building. This option can save indoor space and still provide elevator access.
These options help make it possible to install an elevator in buildings with difficult space limitations.
How to Maintain Your Elevator
To keep your elevator working well after you install an elevator, regular maintenance is very important. We suggest the following steps:
-
Annual professional inspections: Have a qualified technician inspect your elevator once a year to find any problems and perform needed repairs.
-
Keep equipment clean: Make sure the machine room and elevator shaft are clean and free of dust or debris to avoid damage.
-
Test safety features regularly: Check emergency alarms, lights, and brakes often to ensure they work correctly and keep passengers safe.
Following these steps will help your elevator run smoothly and last a long time.
Conclusion
Installing an elevator can greatly improve building accessibility and convenience. By choosing the right elevator, preparing your building carefully, and following proper installation steps, you can ensure a safe and efficient elevator system. Regular maintenance will keep your elevator running smoothly for many years.
If you plan to install an elevator, consider BDFUJI elevators. BDFUJI offers high-quality, reliable elevators with advanced technology and excellent service. Working with BDFUJI means you get professional support from installation to maintenance, making sure your elevator meets all safety and performance standards.
FAQ
Can an elevator be installed in an existing home?
Yes, many existing homes can have an elevator installed. The building needs to be checked for space and structure, but modern elevators can fit into most homes with some adjustments.
Is an elevator installed from the top or through the floor?
Elevators are usually installed from the bottom up, with parts assembled inside the shaft. Technicians often work through the floors to build and connect the elevator components.
Does a new elevator installation need a generator?
Most elevators do not need a separate generator, but having one can provide backup power during outages to keep the elevator running safely.
Is certification needed to install an elevator?
Yes, elevator installation must follow local safety codes and regulations. Certified professionals usually handle the installation to ensure it meets all legal requirements and safety standards.